When selecting a new or used Air Dryer, it is important to consider the type of unit you will use. Some types include Coalescing dryers, Fluidized-bed dryers, and Parallel coils of copper tubing. Some units also use Intermediate media. Learn more about these options and how they can help you achieve your drying goals.
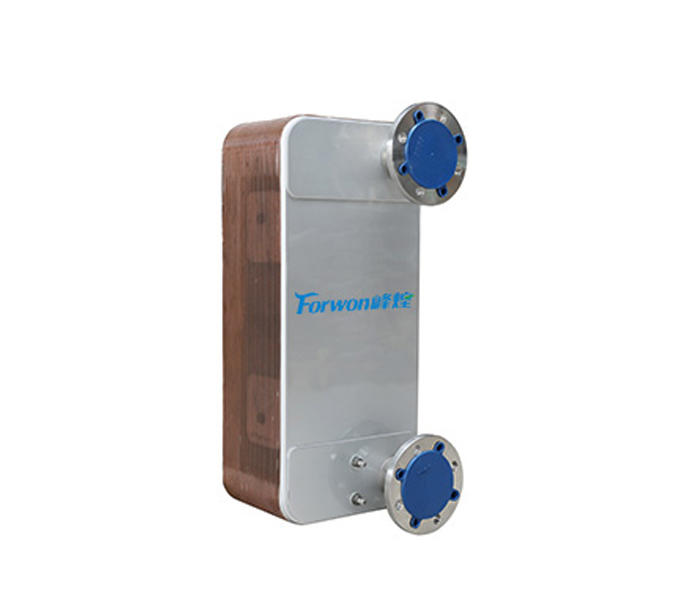
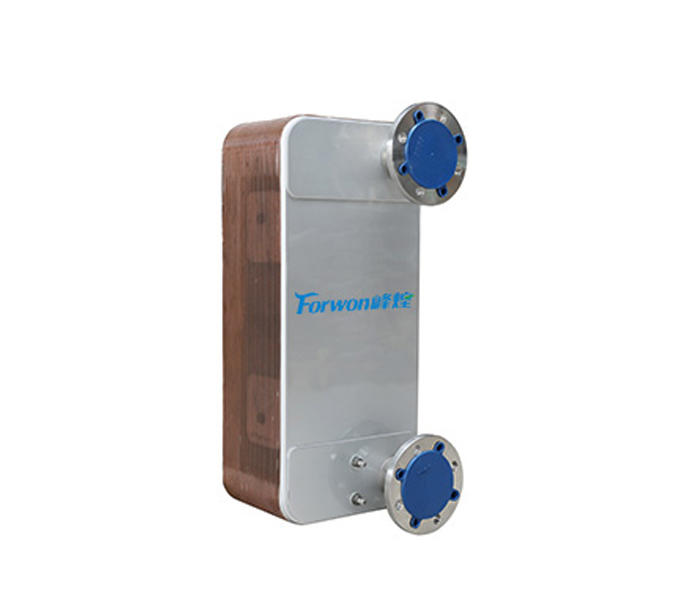
Coalescing dryers are a great way to improve the heat transfer performance of a process by removing moisture, oil, and particulates from the process air. These types of dryers work by trapping sub-microscopic water droplets that are too small to be filtered by other methods. They are also known as filters because of the way they capture contaminants in the air stream and remove them through a series of processes.
Coalescing dryers typically feature a coalescing prefilter to remove particulate matter from compressed air. The compressed air is then fed through an open inlet valve to the tower. Once inside, the air passes through a desiccant to remove water vapor and lower the dew point. The dried air then passes through a particulate postfilter and outlet check valve before exiting the system. A small portion of the dried air is diverted into another tower for regeneration.
In an air dryer, parallel coils of copper tubing are used to heat or cool the fluid inside the dryer. The heat transfer area depends on the overall heat transfer coefficient of the fluid. This coefficient depends on the temperature, density, and transport properties of the fluid. A thermal boundary layer will form on the product side of the coil, which will have a large temperature difference between the surface of the coil and the bulk fluid. The difference will result in large natural convective currents and a high heat transfer coefficient.
The dehumidified air then flows through an intermediate annulus of tubes 16 and header 26'. The dehumidified air is then used for pneumatic systems. Because these components are made from readily available materials and do not require bending, parallel coils of copper tubing have significant economic benefits.
The air dryer is made up of several components: a primary heat exchanger 200, secondary heat exchanger 300, and condense trap 400. The primary heat exchanger is the primary part of the system and consists of a number of plates 210 and 310 that transfer heat to the air. The number of plates can range from four to more than two hundred. The plates are interconnected with sheets of brazing material.
The heating and drying processes are enhanced by the use of high-rate infrared and convection technology. These systems are able to produce uniform heat distribution to a large volume of material. The process is also cost-efficient, because the process uses very little energy.